What Will Future Lab Space Look Like?
Demand for life science facilities is booming. Here’s how designers are meeting the challenge.
Science and the research behind it have been and will continue to be key to addressing humanity’s biggest challenges. The COVID-19 pandemic has pushed the science industry to new heights, while proving that collaborations across research disciplines and geographies lead to more rapid advances. And this winning method is here to stay and grow. But for that to happen, the industry needs the right kind of lab space.
According to CBRE’s most recent figures, in the fourth quarter of last year, a record 31.6 million square feet of life science space was under development—both new construction and conversions—across 12 of the country’s largest markets. There is tremendous interest in adapting existing office buildings and expanding research-capable developments in and near major science clusters. How feasible is it to transform spaces previously used as offices into lab spaces? What are the first things designers and architects think about when designing lab spaces? We tried to answer these questions and many others to catch a glimpse of the future lab space.
Every science has its own lab type
“I want to understand the science first before anything else,” Erik Lustgarten, global sciences leader at Gensler, told Commercial Property Executive. “I ask questions like: What type of technology is being developed here? What are they doing and who are they trying to impact? From there, what technology and materials do they use?” he said.
These questions set ideas in motion about what types of equipment a lab will need, helping architects understand who it impacts and how architecture can best help the scientists through their designs. It’s crucial to consider creating something that can adapt over time as their needs change—essentially to not get in the scientists’ way and make their jobs easier.
Matthew Fickett, principal at SGA Architects, highlighted one main characteristic of lab space: lab buildings and office buildings are dissimilar in general requirements. Specifically, labs typically require higher ceilings than offices, as well as different mechanical shafts and electrical services. Moreover, the needs of particular companies and users also greatly differ as some labs are affected by the light within the space, while others need hazardous material storage rooms or dedicated elevators for companies with animal control facilities.
The focal point of lab design starts with how people navigate that space—how they deal with environmental, health and safety issues like smells and potential flammables, summed up Lustgarten. “We flip it upside down and understand the lab workers and not only solve issues of safety but also the intangibles of how people connect with each other and experience the lab,” he said.
Key drivers for change in lab space design
Expectedly, the main key driver is technology: equipment technology and automation of lab processes, connectivity through the internet, data collection and visualization. Another important aspect is connectivity through interaction among different groups in a research organization, according to Lustgarten.
SGA Architect Partner John Sullivan noticed a shift in the life sciences industry, which is altering the way that lab-office buildings are designed. “The old pharma model of developing large complexes devoted to R&D or manufacturing in suburban clusters has been upended by a new wave of data-driven life sciences companies who want to be located as close to the city as possible, with flexible spaces and shared amenities,” Sullivan added.
READ ALSO: Where Are the Next Life Sciences Hubs?
He went on to explain that these companies are situated along what is called the “drug discovery pipeline.” Some of these firms are start-ups that need bench lab space, but others are mature companies that require a whole floor or campus. “On top of that, is the proliferation of mixed-use buildings with lab-friendly features,” Sullivan noted.
The real estate market adapted to these needs through offers that include perfectly designed spaces with built-in flexibility and speculative labs, to serve companies at every step along the pipeline.
Primary design features of lab spaces
Most R&D tenants in mature life sciences markets are seeking BSL-2 lab spaces—Biological Safety, Level 2—which all follow a similar pattern, according to Fickett.
“Approximately 60 percent are open labs, made up of standardized, flexible benches serviced from overhead or below. These can be removed and replaced with floor-standing specialty equipment or equipment on tables as needed, which is often robotic testing or batching equipment. The other 40 percent are lab support rooms, including cold rooms, microscopy suites, specialty equipment rooms for various imaging or characterization technologies, various supply and waste storage spaces, and multiple tissue-culture rooms,” he explained.
Amenities hold a special place in the design of these spaces and can be a key differentiator because lab tenants are inherently health-driven, so biophilic elements like living plant walls and increased access to daylight and fresh air are important factors. Lab-space tenants will look for features that boost wellness, such as open and accessible stairways, dedicated fitness spaces and showers, healthy food options and even outdoor dining, as well as walking paths and bike storage rooms.
Ultimately, the dream is to truly integrate the workplace with the lab end, according to Lustgarten, and even though it is something the industry is working towards, we’re not there yet. Presently, thermal comfort, heat and humidity control are a must. Good lighting—the kind that is well distributed and doesn’t cast shadows—is also a must. The ability to adapt and be flexible is imperative and, lastly, the capacity to locate safety items as soon as a user enters a space is crucial, as is having easy and intuitive access to personal protective equipment.
Flexibility is king
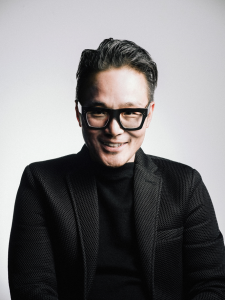
Chad Yoshinobu, Global Sciences Leader & Global Health Sector Leader, Gensler. Image courtesy of Gensler
The health crisis has created a sense of urgency, not just in the search for a vaccine but in real estate development, as well. According to Sullivan, many tenants prefer to rent labs built on speculation, rather than wait for a custom space to be designed and erected. This is one of the reasons why developers often choose to build some or all the lab space at the same time as the base building, which means that they aim for maximum adaptability with modular floorplans, flexible casework and centralized services.
“Flexibility is driven by building grid and grid is driven by lab planning module,” according to Chad Yoshinobu, global sciences leader & global health sector leader at Gensler. At the company’s NEXT lab concept in Seattle’s Uptown Arts District, flexibility is tied to the building grid, and the building layout is determined by the lab bench and the vibrations in the floorplate.
Specifically, the lab bench is where equipment is stored, experiments take place and work is prepped. It is a key building block of any science building. The grid is flexible at 33 feet by 33 feet. “This is optimal for a lab bench layout because it allows our tenants to choose what’s best for them by orienting their lab bench N-S or W-E. This grid achieved a vibration of 6,000 million instructions per second, a go-to standard for most lab buildings,” explained Yoshinobu.
In addition, Gensler’s team relocated the building’s core from the center to the side. “Putting a core in the middle of a building is like putting a fireplace in the middle of your living room. It bifurcates and separates tenants. This move allows our tenants even more flexibility on their layout, without the obstruction of the building core hampering their options,” he added.
Natural ventilation is also highly important for Gensler’s NEXT lab concept, as well as outdoor spaces on every floor. Moreover, the building boasts a multitude of operable windows, which enable access to fresh air. Gensler moved the fire stairs from the building core to the perimeter, which is flooded with daylight and views, turning it into a wellness amenity—no more relying on elevators. Not only was this stair the most underutilized component of the building that now turned into an attraction but with help from access control technology, this arrangement makes the stair an interconnecting one for specific tenants on multiple levels. It also eliminated the construction of costly internal stairs, reduced unnecessary construction, saved money and brought the space to market sooner.
In addition, spaces that promote the health and wellness of their employees and of the communities in which they are located are increasingly on tenants’ radars. A Gensler survey found that one-third of science workers rank outdoor space as their most desired workplace amenity. “It’s no longer a ‘nice-to-have,’ it’s a ‘must-have'”, Yoshinobu said.
At the confluence of location, climate and design
Science labs require consistent humidity and temperature, regardless of their location. Technically, labs are easier to design in more temperate climates. Lustgarten highlights that designing a lab building in the Northeast varies from designing a building in the Southeast simply because the Northeast deals with varying seasonal changes, which affect the design systems and how energy is reclaimed from the exhaust in a building.
“There are also issues related to the scarcity of real estate in parts of the U.S.,” he added. “In urban settings, we see more density and it changes our approach. An example is a building in Philadelphia where we have emergency generators next to a rooftop penthouse on top of the building because the footprint is limited. Conversely, in San Diego or Florida, where land isn’t as urban, it’s more common to put an emergency generator on a concrete pad with an enclosure around it in a parking lot.” There are many regional differences that are both based on the value of land and its availability in the building setting, as well as climatic factors that differ across the U.S.
Temperature-sensitive lab space is among the most challenging to build, irrespective of its location. For example, in an all-glass-façade building, placing temperature-sensitive lab space on the south side can be problematic. This may require the installation of a precise air conditioning system that doesn’t over-cool other rooms that are far from the façade, according to Fickett. “One solution is to wrap the lab in a protective layer of office space as the office can usually swing in both temperature and humidity more than the lab can and serves as a buffer between the sensitive lab and the great outdoors,” he explained.
Rising timber
Steel and concrete remain primary construction materials in the commercial real estate industry, but mass timber in large building construction has become increasingly more popular in recent years, mainly due to its ability to significantly lower the carbon footprint of a project.
“The material also has an emotional appeal because it lends warmth to a building’s interior. Steel and concrete must be covered with extra material to achieve the same result. We also discovered that timber is particularly suited to off-site modular construction,” shared Yoshinobu.
In fact, behind the NEXT lab concept, there was an idea of a Lego building block and, subsequently, the NEXT kit of parts was fabricated in a factory and delivered to the site. Yoshinobu said that NEXT buildings are erected 30 percent faster and are 10 percent cheaper than conventional concrete structures. “With 85 percent fewer deliveries to the site and a 75 percent reduction in construction waste, NEXT emits 80 percent less carbon to build than a conventional concrete lab building,” stated Yoshinobu.
READ ALSO: Spotlight on Arizona’s Pioneering Timber Office Project
Repurposing office
There are 94 million square feet of office space in New York City alone, reported SGA Architects Principal Brooks Slocum. And with office space demand waning lately, Slocum believes that it makes sense for developers in urban areas to resort to conversions. But transforming an existing building into a lab-office space does not only require a substantial investment—including the price tag of the property and the later costs of tenant fit-outs—but it also comes with important architectural challenges.
“Upper floors are sometimes difficult to use for lab space due to chemical quantity restrictions. New mechanical systems to support labs compete for roof space with existing neighborhood site lines, zoning restrictions and structural capacity. New shafts for lab mechanical systems must be threaded through the existing structure and tenants. Sprinkler systems must be upgraded to a higher hazard. Loading docks and material flow paths designed for office buildings are sometimes not large enough or well separated enough for lab use,” Slocum explained.
Lustgarten knows that there is no one-size-fits-all approach to meet every scientific need in a facility, but said that the goal remains to create a framework and strategy that will be responsive to the needs of future tenants.
You must be logged in to post a comment.