Manufacturing Demand for Industrial Space Is Mushrooming
Before the end of this decade, a quarter of industrial demand will be from factories, JLL predicts.
Manufacturing in the U.S. is expanding at a rate not seen in decades, and it is going to have a major impact on the U.S. industrial real estate markets, according to a new JLL report, U.S. Manufacturing Renaissance.
In fact, JLL predicts, manufacturing-related demand will reach 25 percent of U.S. industrial demand by 2028, up from less than 19 percent last year.
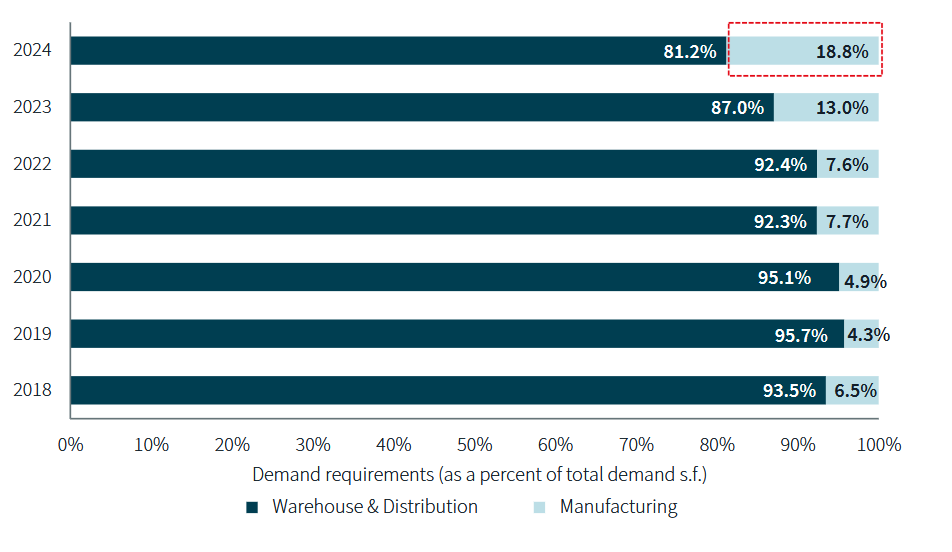
Manufacturing demand for space has already expanded in a major way, the report notes. In 2019, such demand represented only 4.3 percent of total industrial space demand. By 2024, that share was 18.8 percent, well over a three-fold increase.
This is a complete turnaround from before 2020. From 2018 to that year, manufacturing requirements decreased 1.9 percent each year, on average. Since 2020, those requirements have increased by 50 percent each year, on average.
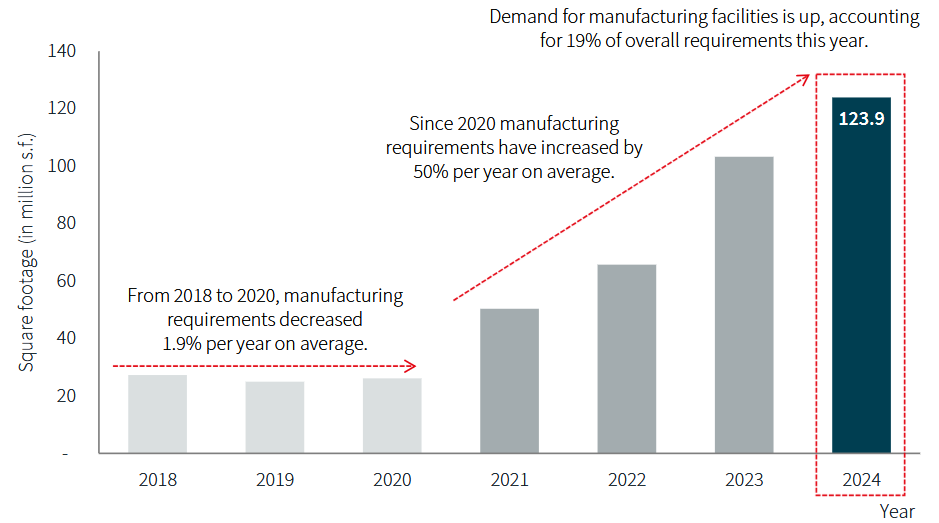
Reasons for the change
“A confluence of economic, technological, and geopolitical factors is compelling manufacturers to reassess their operational strategies and locations,” Greg Matter, JLL’s executive managing director of industrial leasing told Commercial Property Executive.
The resurgence has come from a number of different industries, but the prime driver has been in such industries as batteries and electric vehicles, clean energy and semiconductors. The automotive industry, led by EVs and autonomous tech, is expanding, and so are aerospace, defense and AI.
READ ALSO: Sector Transitions as Supply Shrinks
The demand has been in a lot of places, but major markets such as Chicago, Dallas-Fort Worth and Phoenix are benefiting the most.
A number of factors are at play in pushing up demand for manufacturing space, including reshoring, which is at least in part a reaction to supply chain issues during the pandemic, as businesses seek more resilient and stable supply chains.
“As companies seek to optimize their production processes and bring operations closer to end markets, the demand for modern, technologically advanced manufacturing spaces is likely to continue its upward trajectory,” the report noted.
Political support
Political considerations are also important, and the political will seems to be there to support manufacturing growth.
“Amid the ongoing discourse surrounding tariffs, it is evident that there exists bipartisan support for the ‘reindustrialization’ of American manufacturing,” Matter said. “Our data projections indicate that this trend will persist over the coming decade.”
The new administration is pushing protectionist policies that will likely encourage domestic manufacturing, the report explained. Also, the former administration oversaw policies spurring domestic chip manufacturing and sustainable energy manufacturing, which has momentum that is unlikely to be undone.
New development is in the cards
Satisfying the surge in demand for manufacturing space will be more than a matter of retooling or expanding existing facilities, because the average age of existing manufacturing space in the U.S. is 51 years, with more than half between 30 and 60 years old. That is, they are leftovers from the previous golden age of U.S. manufacturing—before the 1980s.
The bulk of the older facilities are in such traditional manufacturing markets as Chicago, Detroit and New Jersey, which will see both new development and updating facilities to use the latest technologies. Markets such as Savannah, Ga., and Phoenix are leading the way in new facility development.
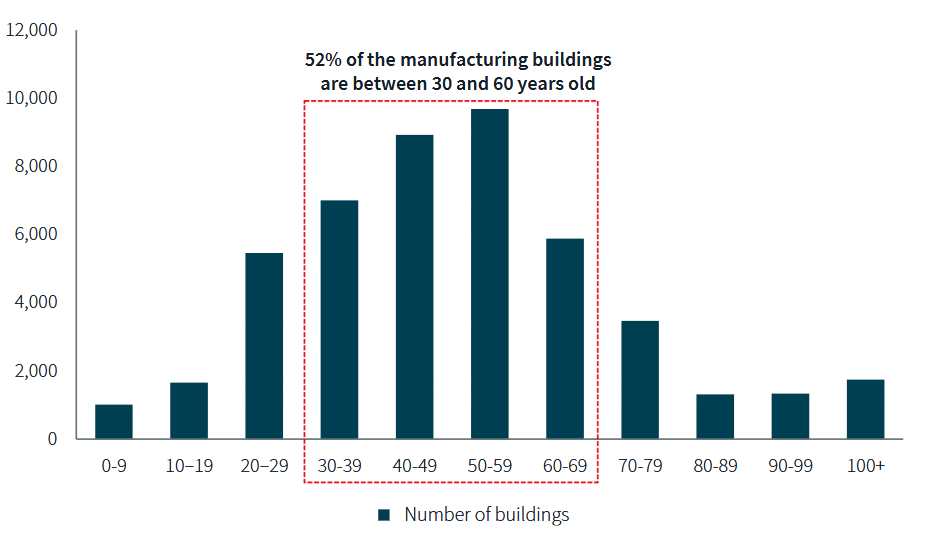
Besides the age of the building stock, other challenges for manufacturing will include finding suitable land, enough power and enough skilled labor, JLL reported.
In terms of land acquisition, a lot of the suitable brownfield sites have already been taken, the result of a “gold rush” for such sites between 2020 and ‘23, the report explained. Much of what is left is functionally obsolete, with the expense of redevelopment enough that greenfield options are also being considered.
As for power, manufacturers will be competing with data centers in the future for access to robust and cost-effective sources of electricity.
Labor challenges
Manufacturers will also be competing against each other for relatively scarce skilled labor, especially as manufacturing processes become more advanced.
“The most significant challenge facing companies as they seek to scale up operations in the U.S. will be the long-term availability of skilled manufacturing talent,” Matter said.
When considering the establishment of new facilities, decision-making criteria are evolving beyond traditional metrics such as job creation, growth potential and industry concentration, Matter noted. Companies are now incorporating quality of life factors to enhance their ability to attract and retain a high-caliber workforce.
You must be logged in to post a comment.