Are Construction Costs Stabilizing?
Development activity is likely to intensify amid labor constraints.
The national average increase in construction costs in the second quarter was 1.12 percent over the previous quarter.
The international property and construction cost consultancy firm Rider Levett Bucknall’s latest quarterly cost report shows that year-over-year, the U.S. national average increase in construction costs is approximately 5.41 percent; compared to 5.85 percent year-over-year in the first quarter.
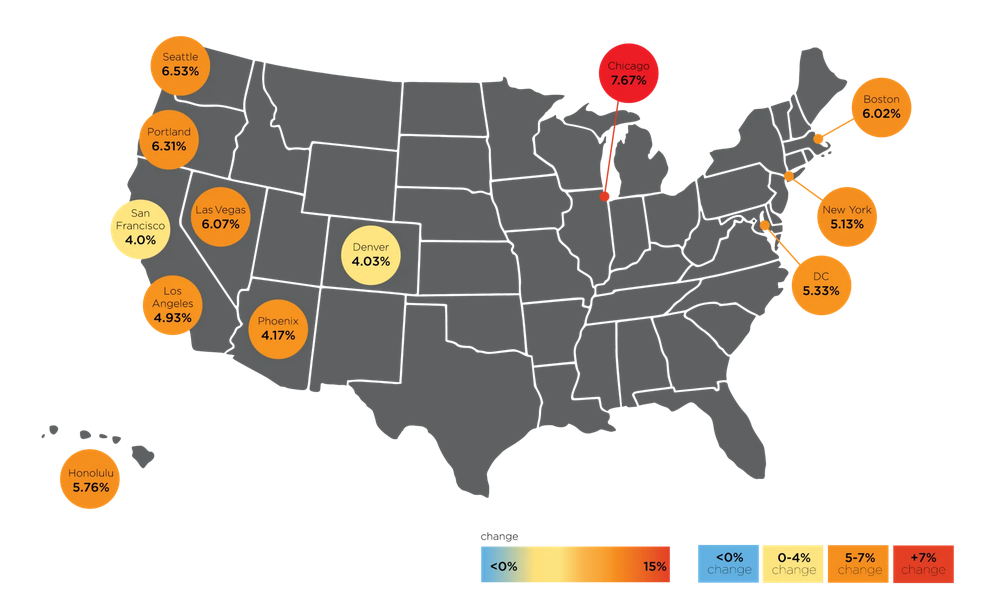
The first quarter showed construction costs rising by 1.31 percent compared to its previous quarter.
RLB’s report features construction cost information for 15 U.S. and Canadian markets and provides a statistical view of the state of the construction industry, detailing indicative construction costs across eight building sectors.
Costs in Boston, Chicago, Denver, Honolulu, Los Angeles, Portland, San Francisco and Washington, D.C., rose compared to the national average this quarter. Denver, Las Vegas, New York, Phoenix and Seattle saw gains that were below the national average.
Demand is strong, but uncertainty is being created by high interest rates and a forecast for increasing labor costs for the rest of 2024, according to the report.
READ ALSO: The New Normal Rate Regime
The unemployment rate for construction is down slightly and sits at 5.4 percent in the second quarter; down from 5.6 percent in the same period last year.
Labor costs are up, partly because the construction industry’s wage premium has decreased in recent years compared to other sectors such as retail and logistics where wages have risen more quickly, according to the report. This implies that wages must increase for the construction industry to attract more workers, according to RLB.
The Architectural Billings Index is 42.4; a decrease of nearly 6 points over the previous month.
Materials costs have cooled from peak
Sandy Romero, research manager, Cushman & Wakefield, told Commercial Property Executive that as inflationary pressure and supply chain constraints decreased, construction material costs cooled from their peak highs.
“Overall construction cost increases have also receded from recent highs, but robust demand and construction labor constraints means that costs will continue to increase, albeit at a slower pace,” Romero said.
“Looking to 2025, expected interest-rate decreases by the U.S. Federal Reserve could result in projects that have been sitting on the sidelines to get off the ground. This may apply additional upward pressure to costs as competition for labor and supplies increases.”
Jorge Serna, who leads Integra Investments’ construction business vertical Integra Build as executive vice president, told CPE that as the second quarter concludes he is seeing the pricing trends from the past six months mostly stabilize across several key trades, such as concrete, aluminum and glass, electrical, flooring, lumber, drywall and plumbing.
“The competition in the market has improved as general and trade contractors’ backlogs burn off, enabling better negotiations with vendors and manufacturers to stabilize or reduce costs,” Serna said. “In 2025, we anticipate continued market corrections that will further improve construction costs, making projects more viable.”
Prices to accelerate in 2025
Andrew Volz, research manager, Project and Development Services, JLL, told CPE that nationally, construction cost growth has slowed below the expected pace of JLL’s forecasts for 2024 made earlier.
“Material prices are in a period of stability and contractors’ focus on the future—specifically developing strong backlogs and retaining labor talent—has regulated the total increase at some cost to margins,” Volz said.
“However, price increases will continue through year-end and likely accelerate some in 2025 as labor supply issues exert upward pressure on costs, demand for new materials evolves, and starts ramp up. The varied trends in development across the country, and their consequences on regional construction costs, underscore the need to engage local market nuances early in the project process.”
Tracy Hunt, executive vice president & general manager for Florida, Skanska USA, told CPE that he has seen some leveling off in construction costs for the first time, which can be attributed to elevated interest rates impacting project financing and the shift toward remote work affecting the commercial real estate office sector.
“This has led to more predictable contractor bids for ongoing projects,” Hunt said. “However, some geographic markets still feel the pressure of unusually heavy construction volume and labor resource constraints.
“While some trades are stabilizing or decreasing, mechanical and electrical trades are still impacted due to the growth in data centers, health care and EV facilities, causing labor shortages and higher wages. Materials for these trades have also been affected, with mechanical supply improving but electrical lead times remaining lengthy, more than 52 weeks, due to data center demand.”
Despite the recent drop in raw material prices for copper, resins and steel, Hunt anticipates a 3 percent to 6 percent price increase over the next six to 12 months due to inflation.
Manufacturers are still facing high demand for all genset sizes and expect prices to rise by 10 percent to 15 percent, according to Skanska’s Construction Market Trends winter report. Additionally, the strong demand from data centers is consuming much of the air-cooled chiller supply, extending lead times to 50 weeks to 65 weeks.
Labor shortage found in Florida
In Florida’s construction industry, one of the primary challenges remains securing qualified labor, Hunt said.
“Material availability in the region appears to be balancing out and many supply chains have managed to revert to pre-Covid lead times,” according to Hunt.
“Currently, subcontractors specializing in electrical and drywall work are reluctant to take on large-scale projects, preferring instead to focus on specific components rather than committing to entire projects spanning two to three years due to fluctuating labor and construction material costs.
“This trend requires breaking down trade packages into smaller components, requiring the hiring of multiple partners for flooring, electrical work and drywall installation,” Hunt said. “As a result, there is a growing need to expand project teams to manage these increased complexities effectively.”
The number of building permits issued across the U.S. in May was at their lowest level since mid-2020, according to Jeff Brown, founder & CEO of T2 Capital Management.
He told CPE that with construction activity now back in line with 2019 figures, the downward pressure on both labor and material costs continues to intensify.
READ ALSO: It’s Time for Investors to Get Off the Sidelines
“Looking ahead, it seems plausible to see material prices continuing to fall in concert with the receding demand,” Brown said. “Even with that reprieve, the cost of capital as well as insurance remains elevated, which hampers the economic viability of new construction projects, thereby further pressuring material costs to the downside.”
This year in Boston, the construction market has been navigating fluctuating costs, according to Matthew Guarracino, principal & CEO of JM Electrical.
“Materials have seen price hikes due to supply chain disruptions, and while some sectors report challenges with labor shortages, our industry benefits from a robust pool of skilled workers ready for deployment,” he said.
“Despite these initial challenges, we’re optimistic about stabilizing costs as supply chains improve.”
In Chicago, Steve Wiley, senior vice president, McHugh Construction, told CPE that construction prices are ticking up at a more modest rate than the spikes the market experienced from 2020 through 2022.
The price of construction materials and services used in nonresidential construction increased 0.4 percent from March to April, according to an analysis completed in May 2024 by the Associated General Contractors of America.
“Longer manufacturing lead times and higher levels of supply chain stress are causing higher construction prices,” he said. “Also, higher interest rates and larger equity requirements for developers and owners add to budget challenges and are stalling some projects. Despite these trends, developer interest in new projects remains strong.”
Construction machinery, equipment costs spike
Robert Martinek, director at EisnerAmper, told CPE that the COVID-19 pandemic created supply chain disruptions, which led to a spike in material costs.
“Although material costs such as plastic construction products, lumber, plywood and steel mill products have dropped due to an improving supply chain, construction machinery and equipment costs have continued to increase through 2024,” he said.
A shortage of skilled workers is one of the primary drivers of increased costs, Martinek said.
“The construction industry has struggled to attract new talent, leading to higher wages as companies compete for a limited pool of qualified workers,” he said. “The shortage is exacerbated by an aging workforce, with many experienced workers retiring without enough new entrants available to replace them.”
READ ALSO: Are Microgrids the Answer to CRE’s Power Struggle?
“High interest rates increase the cost of a construction loan, making it more expensive to finance projects. Additionally, developers and contractors have been dealing with rising inflation. Although there are calls for the Fed to reduce interest rates, many builders are not expecting large interest rate reductions in 2024-2025,” Martinek added.
Many environmentally conscious consumers are looking for sustainable materials and energy-saving technologies, according to Martinek. “However, insulation materials have increased raw material costs for energy-efficient buildings. While technology in construction promises efficiency and sustainability, often, the upfront spending for these technologies may initially raise construction expenditures.”
“Unless rents can be increased and expenses decreased, the rising costs in commercial construction may slow the pace of new buildings in 2025. To date, residential builders have been able to pass through cost escalations due to a housing shortage and sustained demand. A decrease in labor costs and interest rates should lead to further demand in residential and commercial construction,” Martinek concluded.
You must be logged in to post a comment.