Avoiding Delays in Large Construction Projects: 6 Tips
These ideas will help you save time and money, says Sandy Hamby of MOCA Systems.
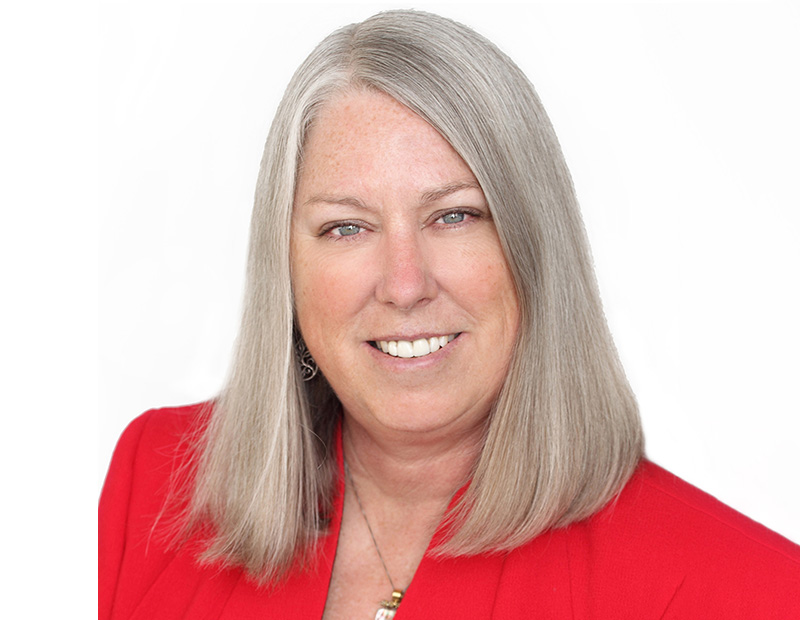
Research from McKinsey reveals that large construction projects often take 20 percent longer than scheduled, contributing to budgets exceeding their original estimates by up to 80 percent. Such delays have significant financial and operational impacts.
Owners can avoid such costly delays by taking a proactive approach to vetting schedules to ensure all required knowledge is available during their creation.
Delayed projects negatively impact everyone involved as costs go up; general conditions payments increase; liquidated damages payments may be paid by general contractors or mechanical, electrical and plumbing contractors; and revenue is lost by owners who are not getting the benefit of the completed building.
When a sound schedule is created, owners will have greater confidence that their project will finish on time. They will also have the visibility needed to identify and quickly address problems that will inevitably occur. Here are some best practices to keep projects on schedule.
READ ALSO: Will Your Construction Costs Go Up in 2025?
1. Begin with a timely, realistic, validated baseline schedule
When a project starts, the GC creates a baseline schedule that outlines the project completion plan and how long it will take. In large projects, this schedule is a roll-up of numerous other schedules that describe the work of multiple contractors and trade teams.
The first action owners should take to ensure a sound starting baseline is to actively monitor the progress of creating this schedule and set clear requirements for the GC for what the schedule should contain and when it should be completed.
2. Be mindful of hidden dependencies
Creating a high-quality baseline schedule requires both an understanding of construction and mastery of appropriate scheduling software. In delayed projects, the most common issue is that schedules are created by merging all the sub-schedules but fail to account for important logical dependencies among different parts of the project. Construction expertise is applied to the schedules, but if dependencies are missed–such as sequencing work for complex installations or supply chain problems–these missteps create added cost and delays.
Schedules should be validated by experts with deep experience in construction management who can identify hidden dependencies and provide guidance by the scheduling software expert to make sure the schedule correctly reflects them.
3. Build in and track float time
By clarifying what the baseline schedule should contain during creation, owners will avoid future problems. While most baseline schedules focus on the critical path, they often miss crucial elements such as permit acquisition, inspections and procurement of equipment and materials with long lead times.
Baseline schedules should be cost-loaded, aligning scheduled expenses with the budget to prevent the occurrence of inflated and unexpected costs that will reduce scope. And the baseline schedule must validate planned costs against the project scope to identify design elements that may be too costly to fulfill.
Owners should insist on tracking float, i.e., the time an activity can be delayed without affecting the project’s completion. If float is not tracked and managed, items will unexpectedly impact the critical path, causing delays.
When the float starts getting low, the schedule is in danger of slipping.
4. Complete schedule as early as possible
Baseline schedules are complex and may take months to create. Often, by the time they are delivered–sometimes six months after a project starts, work is already behind.
Owners should press for the completion of the baseline schedule as early as possible and request a placeholder schedule within two weeks of project kickoff, outlining the scope and detailing tasks for the first 90 days. Owners should also press the GCs to update the baseline schedule as the project progresses.
5. Be realistic when allotting task times
The baseline schedule should be realistic for how long each task will take. We see projects that build in too much margin by doubling the time needed to get the building under roof. Conversely, arbitrary cuts to task durations are sometimes made to meet deadlines without assessing feasibility. A realistic schedule incorporates knowledge of reasonable timeframes based on experience and the specific conditions on the project.
6. Update the schedule regularly
Even the best-validated schedule is only a starting point. It must be regularly updated to reflect reality–bad weather, supply chain issues, lack of manpower, change orders and more.
Timely synchronization of progress on the job site with the schedule avoids these problems and highlights opportunities to save time and money.
Owners will significantly reduce the risk of delays and increased costs with a timely, realistic, validated and continuously updated schedule. Such a schedule builds confidence among all project stakeholders. And when the unexpected occurs, the owner will quickly get answers about how the schedule will change.
A well-prepared and actively managed schedule not only ensures a smoother construction process but also lays the foundation for successful project delivery.
Sandy Hamby, AIA, CCM is president & CEO of MOCA Systems Inc.
You must be logged in to post a comment.