Catalyst for Change
Passive House principles, net-zero energy operations and innovative materials will characterize a pair of ultra-sustainable neighboring buildings in the University District of Spokane, Wash.
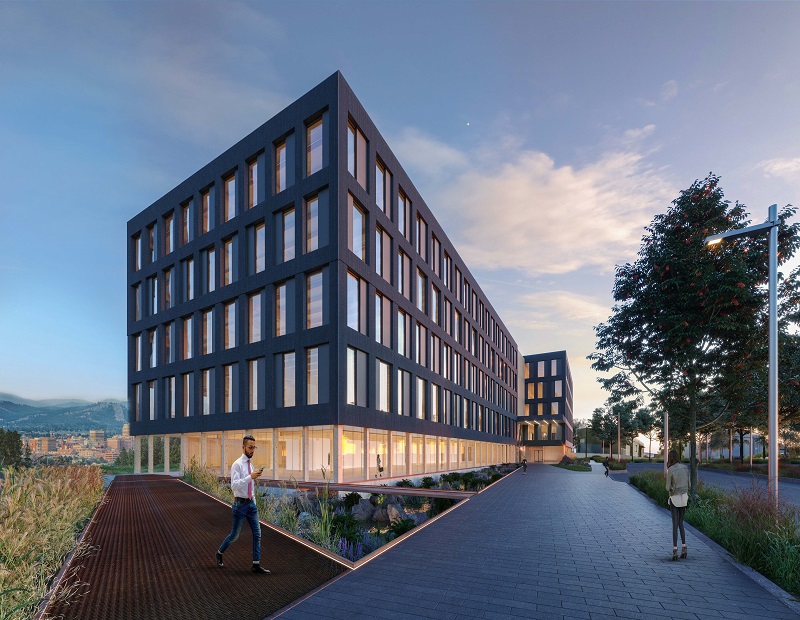
Catalyst, under construction in Spokane, Wash. Rendering courtesy of McKinstry Co.
On the surface, two neighboring buildings in the University District of Spokane, Wash., will look deceptively ordinary to the casual observer when they open in 2020. But Catalyst and Hub represent state-of-the-art strategies for energy operations and construction materials.
A joint venture of McKinstry Co. and Avista Corp., the project consists of two buildings at the South Landing of the new Gateway Pedestrian Bridge in Spokane’s University District. Catalyst, a five-story, 159,000-square-foot building that will include offices, classrooms, common study areas and dry labs.
Catalyst’s lighting, occupancy and plugged-in loads will all be closely monitored, said Ash Awad, McKinstry chief market officer. The result will be a structure using about 35 percent of the energy consumed by a conventional similarly-sized building.
Starting in the fall of 2020, Catalyst will host Eastern Washington University classes. The property will anchor an innovation center intended to cement Spokane’s status as an emerging tech center.
Across the street will be Hub, a 40,000-square-foot companion building featuring a restaurant, offices and a generating plant that will power both buildings. Hub’s first floor will be an “eco-district.” Between them, Catalyst and Hub represent a $100 million investment. They are anticipated to be complete in mid-2020.
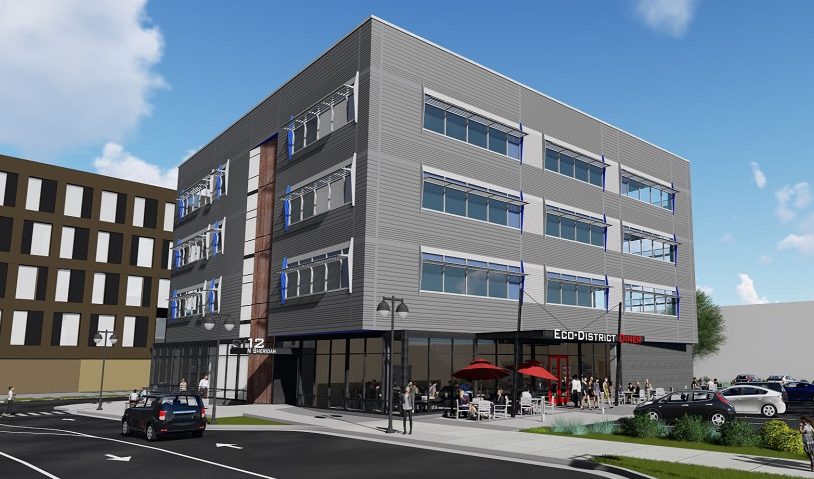
Hub rendering. Image courtesy of McKinstry Co.
No fossil fuel will be burned in the power plant, according to Michael Frank, vice president of engineering and design for McKinstry. “It’s all electric, using a combination heat pump technology [including] both air-source heat pumps and heat recovery chillers so it can heat and cool simultaneously, as opposed to dissipating heat into—or taking heat from—the atmosphere,” he said.
The plant’s thermal storage devices will make it possible for the building to store hot water and chilled water. Electrical batteries will be part of the plant as well. Deployment of both thermal and electric batteries will facilitate movement, storage and sharing of energy. All electric power coming into South Landing will be funneled through the Hub’s eco-district before being redistributed to the campus, Frank reported.
When people consider developing a net zero-energy project, they often assume that the cost will be much higher than for conventional construction, Awad said. “We started with the thought we [would] think differently as to our partners, think differently about our outcomes, and then think about eliminating the inefficiencies,” he said. “And when you do that you wind up with a very different set of outcomes.”
High-tech timber
Among Catalyst’s innovations will be the use of cross-laminated timber, a strong lightweight alternative to conventional poured concrete and steel framing. CLT offers benefits to acoustical, thermal, seismic and fire safety performance. The use of timber is a win from the standpoint of carbon sequestration. “Then, when you compare the amount of carbon emitted through the process of making steel and concrete versus processing wood, it’s another win,” Frank said.
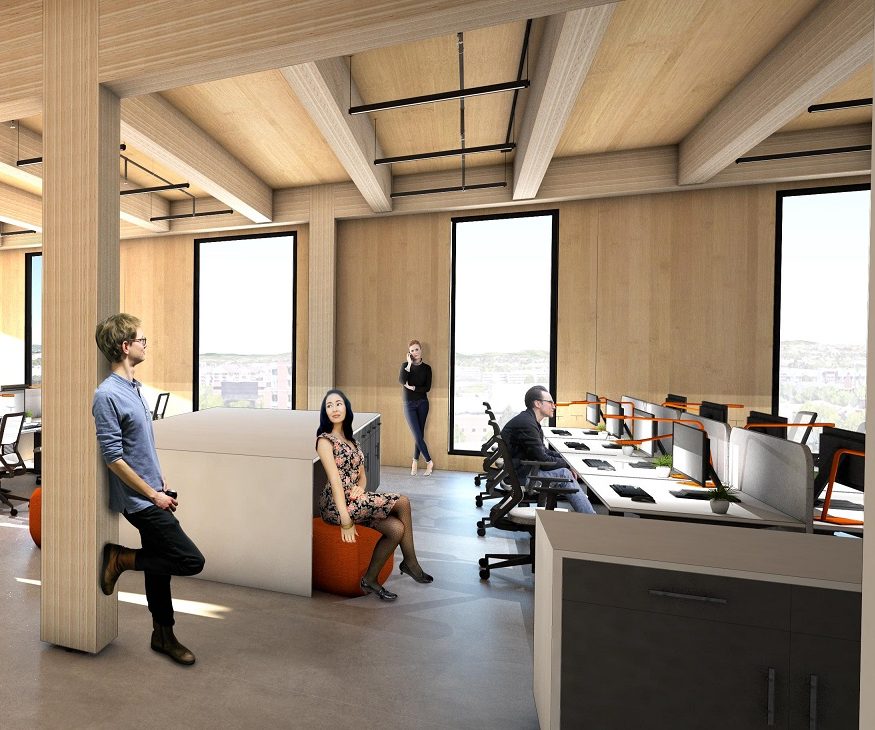
Catalyst Building interior. Image courtesy of McKinstry Co.
CLT will also be used in the exterior envelope of the building to create Passive House conditions, reducing internal and external heat loads to as close to zero as possible. “Using CLT means you have very few thermal bridges in the building, as opposed to curtain wall systems in typical office buildings,” Frank reported. “CLT affords you the opportunity to have a very robust thermal envelope.”
A development partner, Katerra, will harvest the timber from local farms and manufacture the panels in its Spokane Valley plant. “Spokane, Washington has been a timber-supported region for eons,” said Latisha Hill, senior vice president, Avista development and Avista Corporation director. “It’s part of our DNA, and it is cutting-edge.”
The use of timber is a win from the standpoint of carbon sequestration. “Then, when you compare the amount of carbon emitted through the process of making steel and concrete versus processing wood, it’s another win,” Frank said.
Among other sustainable features, Catalyst will include rainwater recovery for a gray water system within the building. Low-flow plumbing fixtures will conserve water. Shower rooms will encourage biking to work. And a smart building management system will maximize building operations efficiency, leveraging use of thousands of IoT sensors, as well as data visualization made possible by machine learning and AI.
You must be logged in to post a comment.