Mass Timber’s Growing Appeal for Builders
Though still small in number, projects using this innovative technique offer a sustainable and efficient solution.
Mass timber construction is on the rise. Once a specialty product found mostly in the multifamily sector, mass timber is now expanding its profile in the commercial sector. The overall numbers are small but increasing steadily. According to a September 2024 estimate by WoodWorks, the number of projects using mass timber has increased nearly 10 times to 2,253, including 306 in the office, industrial and retail sectors.
What explains this uptick? It’s a combination of engineering advances, domestic sourcing, plus critical building code changes that allow projects to get increasingly spacious. Mass timber buildings are widely regarded as considerably more sustainable than their concrete and steel counterparts. Developers have taken notice, seeing mass timber as an attractive option for meeting the challenges of construction efficiency, sustainability and tenant appeal.
Concerns about fire safety and structural stability have historically limited the scale of mass-timber projects, and most projects are still relatively low-rise. But a landmark change in the 2021 International Building Code, which is widely used as the model for state and local building authorities, allows the use of mass timber in structures up to 18 stories tall. Some buildings are now exceeding that height. Ascent, a 25-story Milwaukee residential tower, set the world record when it opened in 2022.
Today’s designs also address concerns about fire safety. As the Wood Products Council notes, large timber elements keep their load-carrying capacity longer than those with small cross sections. As a result, “a char layer forms on the surface while the interior remains undamaged and structurally sound.”
Streamlined supply chain
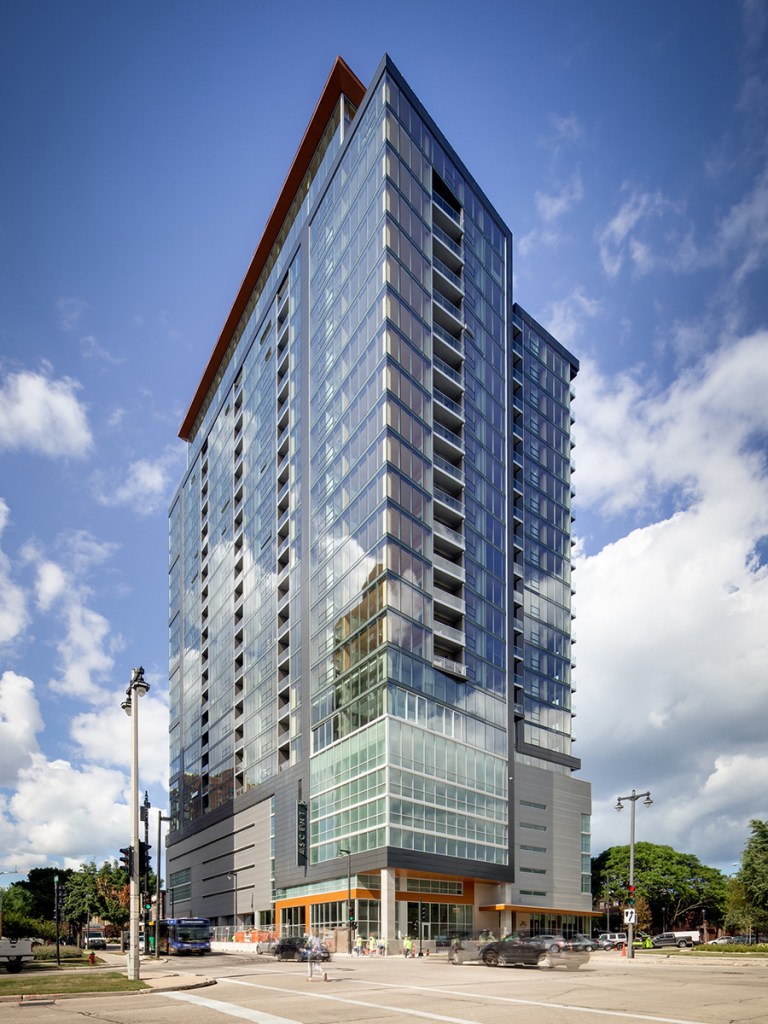
One area to catch the eye of developers has been the construction process, which is significantly faster, less carbon-intensive and less disruptive for mass timber than conventional methods. Building with custom cross-laminated, dowel-laminated or glue-laminated panels is more akin to assembly from a kit than a large-scale construction site complete with concrete pouring and steel welding.
Building with a smaller team may save time and money at a time when the U.S. construction industry is short more than 500,000 workers. On average, mass timber projects go up 25 percent faster than concrete and steel buildings, leading to faster occupancies and less construction traffic.
That was a key takeaway from the development of 619 Ponce, part of Jamestown’s Ponce City Market redevelopment in Atlanta. Completed in early 2024, the 120,000-square-foot office building rose at the same time as a neighboring 405-key hotel with a cast-in-place concrete frame.
“The visual of the differences in what it takes to construct them was incredible,” said Catherine Pfeiffenberger, managing director & head of development and construction at Jamestown. On the site of the 21-story hotel, a dozen concrete trucks and a crew of 120 would gather. “Right next door, there was one truck that would come in, loaded with CLT panels designed to go up in the way it was being installed,” she recalled. “It would drop the panels, finish the floors and leave—all with six people on-site.”
The wooden frames allow for a much faster installation of finishes, which don’t require caulking and paint. “Once you construct a floor you can get directly underneath it, and start putting in finishes and your façade so that you can continue not just the structure but the rest of the building,” said Jordan Komp, principal & director at the Milwaukee office of Thornton Tomasetti. His team provided structural design, engineering and inspection services for Ascent.
Efficiency also characterizes fabrication of the building’s components. “The connections are pre-engineered, pre-drilled and pre-designed so that when the material actually shows up on the site, there’s very little construction waste at all because all the pieces are coming together,” said Anthony Markese, a principal at Pickard Chilton, which has designed more than 4 million square feet of mass timber projects.
Among them is T3 RiNo, a six-story, 220,000-square-foot building located in Denver’s River North Art District. In 2025, Xcel Energy will relocate its regional headquarters to the property, which is being developed by a joint venture of Ivanhoé Cambridge, Hines and McCaffery.
Streamlined supply chains can also ease the path for mass timber development. Traditionally, mass timber projects outside of the Pacific Northwest were built using timber shipped from Canada or as far away as Central Europe. But that’s changing. Jamestown sourced 619 Ponce’s southern yellow pine from local forests owned and managed by the firm. The wood is milled in Albany and shaped into CLT panels in Alabama.
Start-to-finish sustainability
The sustainable nature of mass timber construction is as big a factor in its selection as the time savings. It starts with harvesting, as it takes the average source forest 14 to 25 minutes to regenerate the wood used for a project, Komp noted.
Local sourcing reduces energy consumption for transporting it to the site, and construction methods require less energy than concrete and steel buildings. That reduces the building’s carbon footprint considerably compared to conventional construction.
Sustainability goals justified the premium costs of Baltic Pointe, Utah’s first mass timber commercial building, according to Gardner, the project’s developer. Located in Draper, Utah, a Salt Lake City suburb, the 136,000-square-foot office building opened in 2022.
“When we began, we started assembling our pro formas in numbers, and it would cost us somewhere in the neighborhood of 5 to 10 percent more to do this,” said David Denison, a senior development manager at Gardner. “But at the time, we felt that the additional costs were worth the sustainability initiative.”
During operation, mass timber buildings are more efficient to heat and cool by way of their natural insulation. They also offer reduced water consumption and can even actively sequester carbon.
“They have a total carbon footprint up to one-third smaller than that of traditionally used steel and concrete structures and the ability to largely enhance energy efficiency, reducing heat flow rates by 400 times when compared to steel and 10 times when compared to concrete,” said Michael Caracciolo, vice president of asset management at Ivanhoé Cambridge. Because timber continues to capture carbon as it ages, he added, the building has 38 percent less embodied carbon than a comparable concrete and steel structure.
Ascent, the 25-story Milwaukee tower, could absorb an estimated 70 to 100 metric tons of carbon over its lifetime. As Komp noted, “That’s the benefit of taking 2,400 cars off the road for a year, or powering 11,000 homes for a year.”
Since timber is typically about five times lighter than concrete or steel, it also allows for faster upgrades. “If you’re renovating and expanding, you are not turning down the carbon that has already been expended,” Pfeiffenberger said. And at the end of a building’s life cycle, timber is less likely to end up in a landfill than concrete.
The sustainable aspect of mass timber is an intangible element that can help win over tenants in a challenging office market, its proponents say. “Not only is the product differentiated and meets our sustainability commitments but there is an operational benefit that they can see in their business and bottom line,” said Travis Guinn, vice president of development and construction at Howard Hughes, the developer of One Bridgeland Green. Timber’s aesthetic quality and power to evoke nature adds to that intangible tenant appeal. As Caracciolo noted, “By fostering a more natural and calming environment, it has been shown to reduce stress and lower heart rate and blood pressure, which plays a large role in elevating the overall quality of life in the workplace.”
You must be logged in to post a comment.