The Next Industrial Hotspot? Head South and Then Some.
This country is emerging as a coveted destination due to nearshoring and other market forces.
It hasn’t been an easy four years for global supply chains, with shocks, shortages and political strife making headlines every other week. Just recently, attacks on maritime shipping in the Red Sea have fueled fears around inflation and supply chain breakdowns, while a longstanding decoupling from China is having growing pains.
“When you take away the labor of manufacturing in China, and then you add to that the challenges of the logistics of having to put all the goods on containers, these all (become) challenges magnified during the pandemic,” weighed in Jeff Small, co-founder & CEO of MDH Partners.

To minimize disruptions and build resilience into their supply chains, corporations are increasingly shifting their focus from convenience (“just in time”) to resilience (“just in case”) and from offshoring manufacturing to nearshoring. Amid that transition, Mexico is a rising star in the industrial real estate market.
READ ALSO: What’s Next for Industrial Real Estate?
Our neighbor to South is surpassing China as the U.S.’ largest trading partner as deglobalization slowly but surely pushes through. In the first seven months of 2023, more than $460 billion in goods were exchanged between Mexico and the U.S., Statista reports.
Industrial real estate investors and developers have noticed that, too. According to Fitch Ratings, Mexico’s industrial market attracted more than $18.6 billion in foreign investment in the first quarter of 2023 alone, a 48 percent increase year-over-year.
Advantages: Tangible and intangible
The Mexican industrial market encompasses 916 million square feet across its major cities, according to Statista. This is only projected to grow, with companies such as Tesla eyeing the market. Elon Musk is considering a $5 billion factory in Monterrey, near the border with Texas, and the local government is ready to sweeten the deal.
For owners, operators and tenants, the advantages are both tangible and intangible. On both ends, the market’s most obvious benefit is its geography, with northern states such as Baja California, Chihuahua, Coahuila and Nuevo León providing proximate shipping and manufacturing. Meanwhile, Mexico City can act as a more centralized base of operations.
READ ALSO: For 2024, Prologis Forecasts Growing Freight Traffic
“It’s available, closer to the North American markets than the Asian ones, and provides an opportunity to get goods just in time,” pointed out Matt Brodnik, chief investment officer, EQT Exeter.
Brodnik’s company owns five industrial properties around Mexico City totaling nearly 3.2 million square feet. Primary uses are logistics and distribution, plus some light industrial. Brodnik drew a contrast with Asia-originated maritime shipping, recently the victim of geopolitical disruptions in the Middle East, as well as docking backlogs at home.
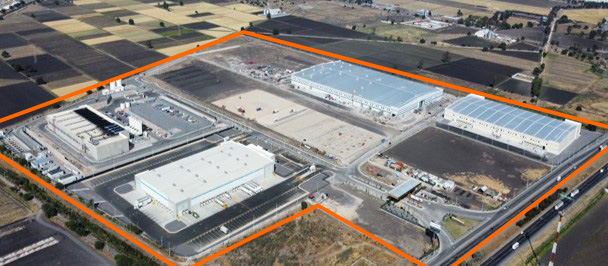
“The closer you are, the better you are able to mitigate (these) from a supply-chain standpoint,” he added.
Andres Correa, director of Latin America corporates at Fitch Ratings, also sees strength in the “regionalization” of logistics and manufacturing.
“Mexico’s proximity is helpful; we have the USMCA agreement that helps it, and more recent policies such as the Inflation Reduction and CHIPS Acts and the Infrastructure Bill have all tricked down to it,” Correa said.
On top of reducing complexities in shipping and manufacturing, industrial facilities in Mexico are also less expensive to operate. Labor costs are roughly 20 percent lower than in China, while the country’s median age of 30.6 years is nearly 10 years below those of the U.S. and China.
“Compared to the U.S. and China, (it has) a good level of education and technical know-how, and there are also good demographics,” Correa added.
READ ALSO: Supply Chain Challenges: The Era of Deglobalization
Energy and transportation costs are lower as well, with electricity rates per kilowatt-hour between $0.023 and $0.107 cheaper. Gardner Ellner, EQT Exeter principal & head of industrial acquisitions, observed these benefits directly.
“We have a project in Cantera where we bought the land and built the infrastructure, and we have a lot of high-power users attracted to the location,” Ellner detailed. “Larger-scale, larger-size goods are much easier to produce in Mexico than to move across the ocean on a ship,” he added.

Proximate prosperity
And it’s not only Mexico proper. Border town-centric developments in Southern California and Texas, which has the highest rent growth in the nation, have increased dramatically over the past two years, with the former having the highest rent growth in the U.S., according to CommercialEdge data.
“There are a number of institutions that have discovered El Paso in the past several months, and what was once a quieter market for industrial in Texas has become one of the most active,” Small said.
For its part, MDH Partners recently acquired a three-building, 555,000-square-foot campus before it finished construction. “A lot of investors are looking at the dynamics and asking, how can we benefit from the growth on our side of the border?” Small said. “(They are) understanding this and asking, what are the stopping points that will benefit from the demand for nearshoring?”
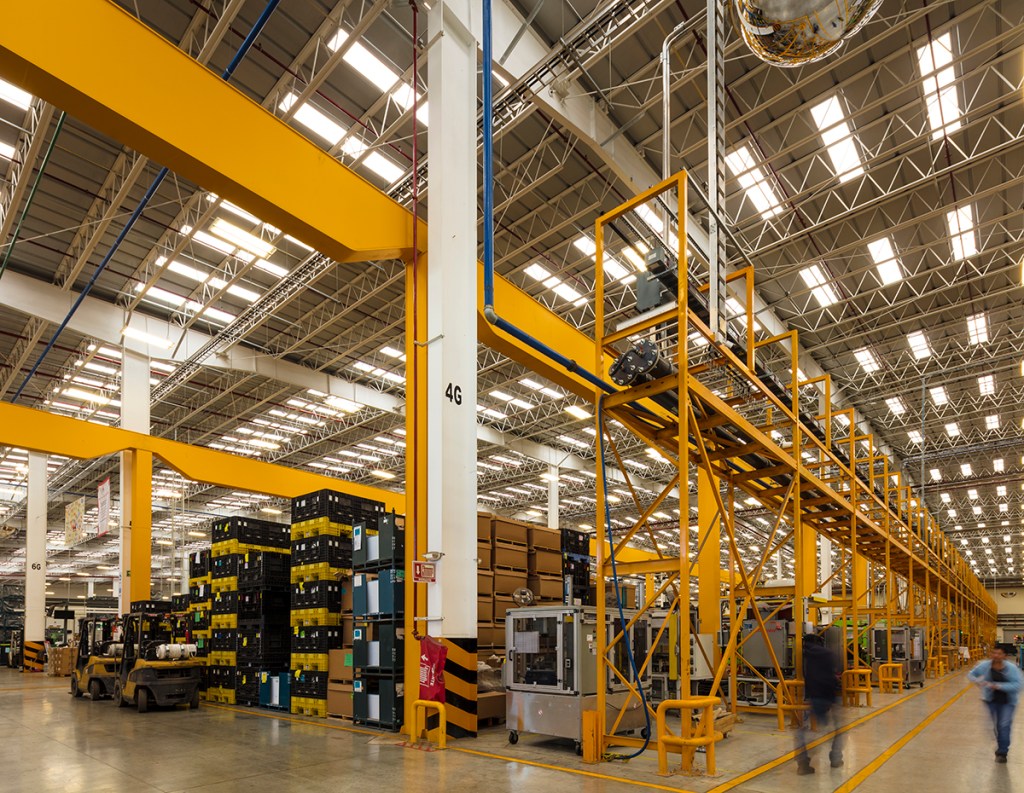
Roadblocks along the way
Despite the allure, owning and operating in Mexico has its unique challenges, most importantly the lacking infrastructure. “For energy alone, in order to support the demand for industrial facilities, Mexico would have to double its generation capacity, and that represents a significant investment in the next few years,” Correa noted.
Meanwhile, roads and transportation remain inconsistent. Ruben Smith, partner-in-charge of the Santa Ana, Calif., office of law firm Frost Brown Todd, has a client building a 3,000-acre industrial park in Baja California, one of the largest developments in the country. The catch? “The infrastructure has not been there,” Smith pointed out.
Having to transport workers can complicate things further. “Under Mexican law, if there is no public transportation to the warehouse that you are working at, the company has to pay for the transportation of the workers, and that can get expensive,” Smith said.
What’s more, some complications are too difficult to simply spend away. Cross-border transactions, as well as land purchase and construction approvals, are fraught with intricacies that only local professionals can understand. W.P. Carey, which has been operating in Mexico for two decades and has a 13-building, 2.4 million-square-foot local industrial footprint, recognizes this.
“You can do a deal in Florida, California or Texas and have a pretty good sense of the differences in jurisdiction among the various states,” said Senior Vice President Jason Patterson. “Cross-border transactions are much more complicated.”
Investors looking to mitigate these issues will need the right legal representation, an understanding of local tax regimes and title law. EQT Exeter, for one, has a local team and emphasizes contractor selection.
With these covered, “we find that building in Mexico is no more challenging than doing it in the U.S.,” Brodnik concluded.
You must be logged in to post a comment.