Ramping Up Warehouse Safety
Industrial owners and operators are sharpening their focus on health and comfort for workers amid pandemic concerns.
Bucking the trends in the office and retail sectors, industrial properties are busier than ever, bolstered mainly by surging e-commerce demand. Net absorption in the sector totaled 268 million square feet in 2020, an 11.4 percent year-over-year increase, according to Cushman & Wakefield.
That trend is powering investment and development in the sector, but it also has far-reaching implications for safety. More goods flowing through the system means more workers and more shifts, and hence more pressure on industrial tenants to provide a safe, comfortable environment for their employees. The risk of coronavirus infection dominates safety concerns at present, but a move to promote healthy workplaces in logistics buildings predates the pandemic.
One issue shaping the trend is the adoption of environmental, social and governance goals. Prologis, to name one major logistics operator, has made a point of pursuing ESG initiatives. In 2018, the REIT opened the first-ever logistics facility to be certified by the International WELL Building Institute. Park Tacoma-Building D in Tacoma, Wash., features natural daylight and an outdoor walking trail in addition to sustainable design features such as energy-efficient lighting.
To some extent, the issue of worker safety is affected by lease terms. Institutional warehouse owners tend to take a relatively hands-off approach, because of the triple-net lease structure that places much of the responsibility for operations on the tenants. The landlord nevertheless has a crucial role to play. Property owners can help tenants on multiple fronts by acting as a sounding board for best practices; directing their customers to specialized professionals; and leveraging information from industry associations as well as from local, state and federal agencies.
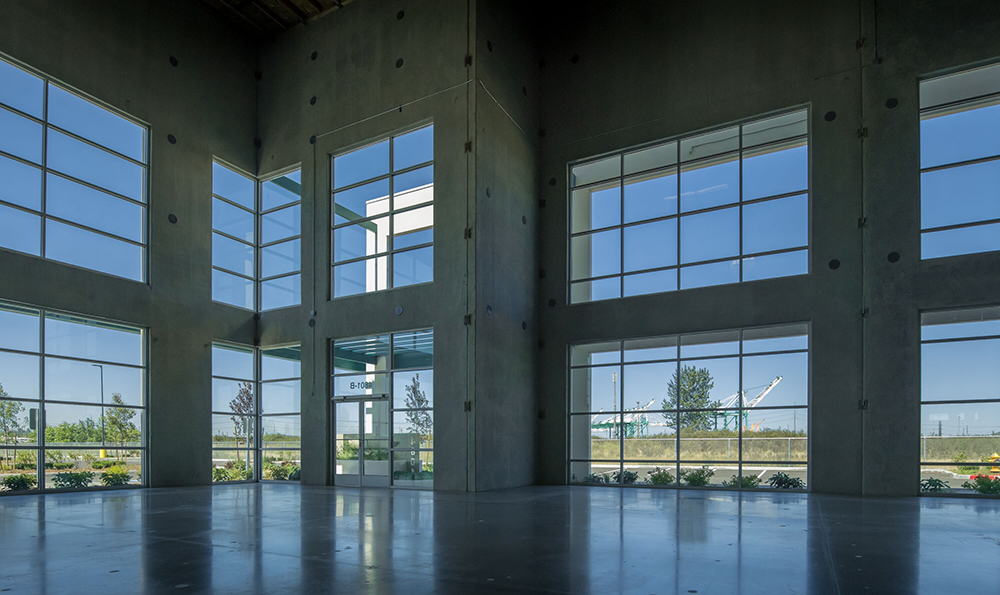
Located south of Seattle, Prologis Park Tacoma-Building D earned WELL certification with elements such as natural daylight and an outdoor walking trail that workers can use during breaks. Image courtesy of Prologis
Air and light
The onset of COVID-19 brought concerns about air ventilation to the fore, leading many industrial tenants to switch to higher-efficiency filters for their heating, ventilation, and air conditioning systems. Depending on the HVAC system’s capabilities, this is often an easy fix to make. “Ventilation has been shown to be critical in improving and reducing the transmission of the virus in work settings,” said Marc Wendell, vice president of health, safety, security and environment for C&W Services, Cushman & Wakefield’s facility services group.
“We want to have at least a MERV of 13,” he added, referring to a filter system’s Minimum Efficiency Reporting Value. Developed by the American Society of Heating, Refrigeration and Air Conditioning Engineers, the standard is defined by the organization as the fraction of particles removed from air passing through a filter. “And we try to ensure that they do as much turnover of air as is reasonable within the work setting,” said Wendell.
Even before the pandemic, industrial tenants were seeking better air circulation to keep workers comfortable in warehouse spaces, which, unlike break rooms and office spaces, are typically not air conditioned because their vast size makes it impractical. One solution that is catching on in many warehouses is the use of enormous ceiling fans to provide cooling airflow during summer or to recirculate warm air during winter.
Some manufacturers are retooling their warehouse products to keep workers safe as well as to improve productivity. Last year, for example, Big Ass Fans added ion disinfection technology to its high-volume, low-speed fans. Each ceiling fan draws air upward so that the UV-C rays produced by the unit kill airborne pathogens, including the virus that causes COVID-19. Disinfected air is then recirculated to the work area. According to the company, the product can reduce the risk of COVID-19 infection by 89.9 percent.
Of note, such products also require a significant investment. Industrial tenants that add fans to a warehouse or upgrade an HVAC system typically foot the bill for the hardware, while the landlord pays for the installation. In that case, the tenant would assume the cost directly or have it amortized over the lease term and paid through operating expenses, explained Jim Clemo, senior vice president & real estate operations manager at Duke Realty. “There’s some flexibility there, but it is driven by the tenant and their responsibility for the space,” he said.
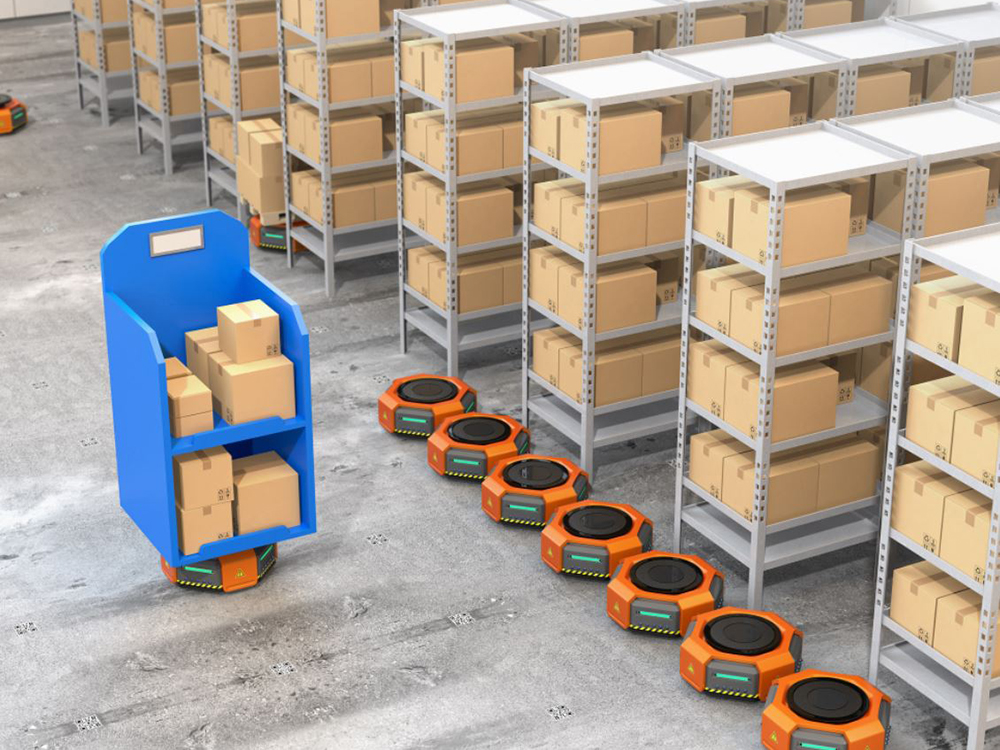
Robots are touted as a way of maintaining social distancing in the warehouse as well as coping with unprecedented e-commerce demand. Image courtesy of Frost & Sullivan
Cleaner spaces and distancing
The pandemic triggered intense interest across the commercial real estate industry in the cleaning and disinfecting of touchpoints as a means of protecting occupants from a contagious microbe. Hygienic concerns are particularly important in industrial facilities, where people must handle materials on-site and frequently share equipment.
“We’re focused right now on ensuring that we have automation in place in a lot of our sites for doing the scrubbing and vacuuming,” said Wendell. “Then our people go through and do more of the touchpoints, where people are potentially going to touch surfaces.”
Those surfaces, he added, are being disinfected with Environmental Protection Agency List N chemicals or disinfectants, which are expected to kill the coronavirus if used correctly. In some cases, the C&W Services team performs multiple daily cleanings of touchpoints and common areas that receive high traffic.
Industrial properties must also address the broader quest for social distancing. E-commerce firms grappling with the combined pressures of surging consumer demand and the need for more physical distancing are starting to turn to robots. Last summer, Gap Inc. augmented the robot fleet at its U.S. distribution centers with 73 units produced by Kindred Systems Inc., a San Francisco-based startup; American Eagle Outfitters added 26 of the robots. Kindred’s SORT systems use artificial intelligence to conduct pick-and-place operations, enabling one worker to manage three to four robots simultaneously rather than standing side by side with other team members.
“Building automation was already a hot point for industrial even before the pandemic,” said Clemo. “Tenants were looking for cost savings on occupancy expenses. They were looking for alignment with their ESG processes and culture.”
In the long term, technology will play an even more vital role in the new era of industrial property safety. Automation could offer a major part of the answer, observe Steve Weikal and James Robert Scott of the Massachusetts Institute of Technology’s Real Estate Innovation Lab in an October 2020 NAIOP report. A study by ABI research estimated in 2019 that the number of warehouses utilizing robots will jump from 4,000 in 2018 to 50,000 in 2025.
Amazon announced to considerable media fanfare last spring that it had developed an experimental robot designed to disinfect large spaces like distribution centers and retail stores. Featured on CBS’ “60 Minutes,” the prototype is capable of autonomously patrolling the aisles of large facilities like distribution centers or retail and emitting ultraviolet light to disinfect. The MIT Computer Science and Artificial Intelligence Laboratory has developed a similar prototype, Weikal and Scott noted.
It may be some time before such technology is widely available as a safeguard for the COVID-19 virus and other pathogens. Investment in these products requires a considerable commitment of time and resources. But in this dramatically changed environment, exploring the options is an emerging part of the industrial operator’s best practices.
You must be logged in to post a comment.